erschienen in der DSAG Blaupause 2016
Michaela Kürschner, blaupause-Redaktion
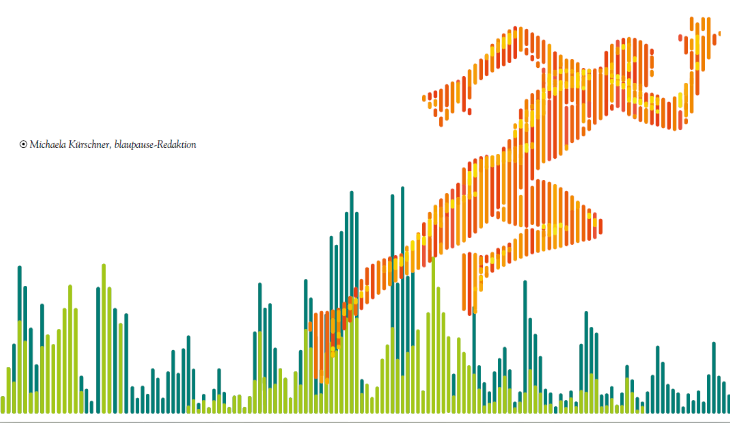
Connected Car, Smart Home, Industrie 4.0: Die Zukunft ist vernetzt –
in allen Lebensbereichen. In Barsinghausen, nördlich von Hannover, hat
ein Mittelständler seine Vision von einer intelligenten Fabrik in die Tat
umgesetzt und dafür die etablierte Anlagentechnik mit dem hauseigenen
SAP-System und einer zentralen Steuerungssoftware vernetzt.
Am Anfang stand der Kauf von drei neuen Zerspanungsmaschinen und die Erkenntnis, dass mehr Anlagen nicht automatisch auch mehr Output generieren. Als Spezialist für Laserschweißen, Laserbeschriftung sowie
Optik und Mechanik stand die Vision Lasertechnik GmbH aus Barsinghausen bei Hannover vor einem Rätsel. „Aufgrund der guten
Auftragslage hatten wir 2014 neue Maschinen angeschafft. Zusätzlich wurden alle Anlagen – sowohl die neuen als auch die bestehenden –
vernetzbar gemacht“, erinnert sich Philipp Becker, kaufmännischer Leiter bei Vision Lasertechnik. Vorhandene Maschinen, die bislang nicht über Netzwerk-Schnittstellen oder einen Ethernet-Anschluss verfügten,
wurden im Zuge eines sogenannten Retrofits nachträglich mit einem smartUSB-Adapter versehen. „Damit konnten sie untereinander
kommunizieren“, erklärt der Manager.
Die intelligente Fabrik ist umfassend vernetzt
Mit der Vernetzbarkeit alleine war es aber nicht getan. „Wir hatten nun also diese smarten Maschinen, insgesamt ist die Produktionseffizienz aber mit den zusätzlichen Anlagen nicht merklich gestiegen“, erklärt Philipp Becker. Bei der Suche nach der Ursache setzte das Team von Vision Lasertechnik
auf Complex Event Processing (CEP), eine Technologie, die Ereignisse zu Gruppen zusammenfasst und somit auch aus großen Datenmengen wiederkehrende Muster herausfiltern kann. Nach vier Tagen CEP- und
Datenanalyse war klar, warum der Output nicht gestiegen war. „Die Zerspaner haben die Zerspanungsprogramme direkt an den Maschinen programmiert, die dadurch ein bis zwei Stunden nichts produzieren konnten“, erklärt Philipp Becker. Nach diesem Vorfall wurde der bisherige Ablauf geändert und die Zerspanmaschinen fortan am PC programmiert
und die Daten anschließend zurück auf die Maschine gespielt.
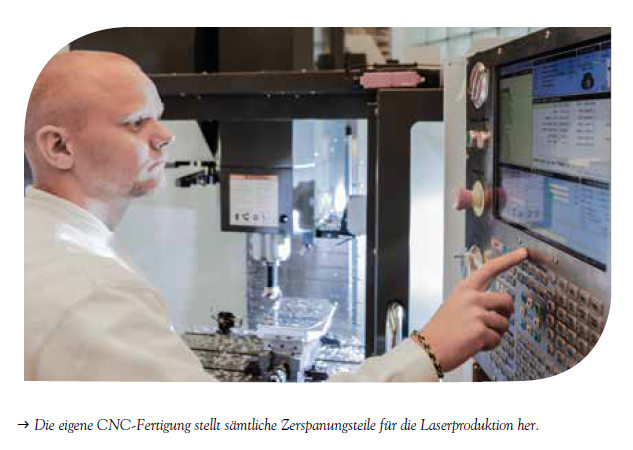
Für Philipp Becker und sein Team war dieses Ereignis ein „Augenöffner“, wie er selbst sagt. Denn aus dem Effizienzproblem erwuchs eine viel grundlegendere Frage: Was wäre, wenn alle am Produktionsprozess beteiligten Einheiten, also nicht nur Maschinen und Sensoren, sondern auch ERP-, PPS- oder MES-Systeme intelligent miteinander vernetzt
wären? Wenn sie nicht nur miteinander kommunizieren könnten, sondern auch voneinander lernen und sich automatisiert steuern?
Und entspräche das nicht der Vision, die die Teilnehmer des vom Bildungsministerium eingesetzten „Arbeitskreises Industrie 4.0“
seinerzeit entworfen haben?
Der Vision von autonomen, intelligenten Systemen, deren individuelle Einheiten nicht nur Informationen miteinander austauschen, sondern die
im Idealfall daraus auch wiederkehrende Muster ableiten und schließlich selbstständig Handlungsweisungen entwickeln?
Das IoT als Grundlage für Industrie 4.0
„Die Vernetzbarkeit und nahtlose Kommunikation vom Sensor bis zum Werkstück sind eine Voraussetzung von Industrie 4.0, aber sie sind noch nicht Industrie 4.0“, betont Philipp Becker. Das Internet der Dinge (IoT)
ist also nur die technologische Grundlage für die „Smart Factory“, nicht ihr Äquivalent.
Smart im Sinne von selbstlernend, selbststeuernd und sich selbst konfigurierend wird sie erst durch die komplette Integration aller
am Produktionsprozess beteiligten Systeme – vom Sensor über die Produktionsmaschine bis hin zum ERP-System. Das war für Philipp
Becker der Punkt, auch SAP mit ins Boot zu holen. „Denn was bringt es uns, wenn wir CEP nutzen und unsere Maschinen Daten austauschen können, aber diese Daten komplett vom ERP-System getrennt sind?“, so
der Manager. Lag die Lösung also darin, das SAP-System über eine Schnittstelle anzubinden, die Daten auszutauschen und fertig?
Ganz so einfach war es dann doch nicht. „Das Problem sind die enormen Datenmengen, die wir verarbeiten“, erläutert Philipp Becker.
„Unsere Sensorsysteme erfassen verschiedene Werte wie Vibration, Position, Gewicht und vieles mehr von verschiedenen Anlagen,
Geräten, Orten und Transportern. Zusätzlich zu den Daten aus den Produktionsanlagen ergibt sich so ein exaktes digitales Abbild der
Produktion.“
Bei diesen enormen Datenmengen gen stößt aber selbst eine Datenbank wie SAP HANA an ihre Grenzen. „Wenn wir beispielsweise mit 1.000 Sensoren jeweils 1.000 Werte pro Sekunde messen, ist das mit der In-Memory-
Technologie allein nicht darstellbar“,
so der Manager. Vision Lasertechnik hat deshalb die In-Memory-Technologie, auf der HANA beruht, mit dem schon in Einsatz befindlichen
Complex Event Processing (CEP) kombiniert. „Durch die Mustererkennung im CEP werden nun wesentlich weniger Werte gespeichert als zuvor“, erklärt Philipp Becker.
Die Folge: Alle ankommenden Daten können in Echtzeit verarbeitet werden.
Selbstlernende Maschinen entlasten die Mitarbeiter
Auf dieser Basis hat Vision Lasertechnik schließlich seine Smart-Factory-Plattform entwickelt. Sie verfügt über Schnittstellen zu den Sensorsystemen und Produktionsanlagen einerseits und zur PPS- und SAP-Lösung
des Unternehmens andererseits und tauscht mit diesen Daten in Echtzeit aus.
„Zusammen mit den historischen Daten aus dem Data Storage kann das integrierte Machine Learning unmittelbar Vorhersagen,
Anpassungen und Muster berechnen.
Auf dieser Grundlage führt die Rule Engine – eine Softwarekomponente, die dem Auswerten von Geschäftsregeln dient – Aktionen aus, fordert also beispielsweise eine Wartung an oder übermittelt einen Alarm an einen Mitarbeiter“, erläutert Philipp Becker. Die Mitarbeiter sind über Smart Watches in den Kreislauf eingebunden. Sie erhalten alle wichtigen
Informationen aus dem Produktionsprozess auf ihr mobiles Endgerät. Die intelligenten Zeitmesser eignen sich gerade im industriellen Umfeld besonders gut, weil sie relativ unempfindlich gegen Schmutz und
Beschädigungen sind und ihr Vibrationsalarm auch bei Lärm erkannt wird. Dabei werden selektiv nur diejenigen Daten übermittelt, die der Mitarbeiter wirklich für seine Arbeit braucht.
„Wenn es einen Fehler an der Maschine gibt, eine Wartung fällig wird oder ein Produktionsschritt abgeschlossen ist, bekommt er eine Nachricht auf seine SmartWatch und kann bei Bedarf eingreifen.“
Die Produktionsanlagen können damit rund um die Uhr laufen, ohne dass ein Mitarbeiter vor Ort ist und ohne dass mithilfe von Kameras die Produktion überwacht wird. Immer häufiger muss selbst im Ausnahmefall kein Mitarbeiter mehr eingreifen, weil auf Basis der Mustererkennung und des integrierten Machine Learnings das System selbst Handlungsanweisungen ableitet. „Der Mitarbeiter lernt vom System und umgekehrt lernt die Maschine vom Mitarbeiter. Entscheidungsmuster
sind dabei nicht fest programmiert, sondern richten sich nach den Vorgaben und Beispielen des Unternehmens“, erklärt Philipp
Becker. Mit der Zeit lernen die Systeme also, schnell und unmittelbar auf alle Eventualitäten in der Fertigung zu reagieren, und schlagen
eine Ideallinie in der Produktion vor.
„Fällt beispielsweise ein Mitarbeiter wegen Krankheit aus, werden seine Aufgaben automatisch an einen Kollegen delegiert. Geht ein Großauftrag ein, werden die Produktionskapazitäten neu berechnet und angepasst.“
Umgekehrt können Fertigungsunternehmen bei geringer Auslastung einen Teil ihrer freien Kapazitäten am Markt anbieten. Das alles passiert automatisch, ohne dass es des Eingreifens durch einen Mitarbeiter bedarf.
Mehr Transparenz über die gesamte Wertschöpfungskette
Durch die Anbindung des PPS-Systems wird zudem jeder Produktionsschritt nachverfolgbar.
„Ein Vertriebsmitarbeiter kann damit jederzeit im SAP-System sehen, an
welcher Stelle im Produktionsprozess sich ein vom Kunden bestelltes Teil gerade befindet“, sagt Philipp Becker. In Zukunft sollen auch die Kunden selbst über einen Link zur Smart-Factory-Plattform live mitverfolgen können, wie viele der von ihnen georderten Produkte bereits produziert sind und wann genau sie ausgeliefert werden. Damit solche Funktionalitäten schon bald zum Standard gehören, arbeiten Vision Lasertechnik und SAP gemeinsam kontinuierlich an der Weiterentwicklung
der Smart-Factory-Plattform. „Die Plattform deckt SAP-seitig alle wichtigen
Funktionen ab, aber es gibt noch eine Reihe weiterer Features, die wir uns wünschen würden“, sagt Philipp Becker. Die Möglichkeit, die Verkaufswahrscheinlichkeit von Lasersystemen auf Basis des CRM-Systems zu berechnen, ist so eine Kann-Funktionalität.
Damit ließe sich vorhersagen, welche Kunden zu welchem Zeitpunkt höchstwahrscheinlich eine neue Maschine ordern. „Wir haben schon
viel erreicht“, resümiert Philipp Becker. So sind alle smarten Komponenten vollständig mit dem SAP-System vernetzt. „Beim Thema Industrie 4.0 sind wir dadurch unserem Wettbewerb ein gutes Stück voraus. Aber wir
müssen auch künftig hart daran arbeiten, dass wir diesen Wettbewerbsvorteil halten.“